Plastic, acrylic and plexiglass – we explain the difference
What is actually the difference between acrylic and plexiglass, and what is the material most used in custom products made by Akriform? We explain the concepts and look at different materials advantages and applications.
Plastic
Plastic is a generic term for a large group of semi-synthetic or synthetic materials. Plastics consists mainly of one or more polymers mixed with additives. A polymer is a large molecule composed of many small identical molecules bound together to form a long chain. These small repeating molecules are known as monomers. By varying the additives used, the nature of the monomers and how long the polymer chain is one can obtain a variety of types of plastic with many different uses. This, as well as the fact that plastics become easier and easier to recycle, has resulted in plastics becoming an indispensable part of modern society.
Plastics are divided into two main groups; thermoplastics and thermosetting polymers. Thermoplastics are plastics that after being formed can be melted down again and re-used. Thermosetting polymers, however cannot be melted down again after curing without its chemical structure being destroyed.
Acrylic
One of the most common thermoplastics is acrylic. The chemical name for it is polymethyl methacrylate (PMMA). PMMA was invented in 1933 by Otto Röhm, the founder of the plastics company Röhm and Haas. Röhm tried to create a lamination between two glass plates to increase the glass resistance, but instead he found that he had developed a completely new glass-like material. Acrylic sheets are easy to glue and are good for milling, bending and hot forming and is therefore a material suitable for many different applications. The material became available for commercial use in 1936 under the protected trademark Plexiglas®.
Plexiglas
So, what is commonly known as “Plexiglass”, is really a brand of acrylic (PMMA). Over the years, Plexiglas® has been developed to cover a wide range of application areas. In its basic design it is completely colorless with excellent optical properties, but the material can be colored in an infinite variety of colors. Today PMMA (“plexiglass”) is sold under many different brand names, including Acrylite, Lucite® and Perspex®.
Other common plastics
Polycarbonate (PC). A transparent thermoplastic with exceptional durability sold under different brands including Makrolon and Lexan. Because the PC is easy to work, mold and thermoform it is used for a variety of purposes, in the construction industry and for safety glass among other things. PC looks a lot like PMMA/plexiglass, but is stronger and can be bent at room temperature.
Polyvinyl chloride (PVC). One of the most widely used plastics found in many different applications in our society, such as in floor materials, hoses and pipes for water supply and sewerage.
Polyethylene terephthalate (PET / APET). Belongs to the group polyesters and is one of the most encountered plastics in everyday life. Main applications include synthetic fibers for clothing and containers for liquids, but also for food packaging.
PETG. A modified kind of PET, with the significant differences that PETG contains glycol. By modifying the PET to PETG the material can withstand higher temperatures without crystallizing, becoming brittle and white. PETG is impact resistant and has very good thermoforming properties. PETG is also suitable for digital printing and is therefore a material that is suitable for product displays, signage and display materials.
Acrylonitrile Butadiene Styrene (ABS). An amorphous styrene-based thermoplastic with high impact resistance and stiffness and good properties for thermoforming. ABS is used for eg machine guards, roof boxes and advertising and the most popular type of plastic when it comes to electronics or engineering applications.
Akriforms custom production
With over 50 highly skilled employees and a full-scale machinery for processing plastic sheets, rods and pipes, Akriform can do basically anything in plastic. From idea to finished product – we can help you all the way. Read more about Akriform’s custom production, the different plastic materials we can supply you with or contact us directly.
Our process
With over 30 years in the plastics industry, we have the experience needed to select the plastic that best suits your project. Most of our custom made products are made of PMMA (acrylic / plexiglass) and PETG, but in many cases they also consists of several other components such as wood, metal and print. For the things we cannot do ourselves we use a number of skillful subcontractors.
When we customize something for you, it is usually done in 5 steps (see below). If you already have a finished drawing, you can jump straight to step three or four, and we’ll do it from there.
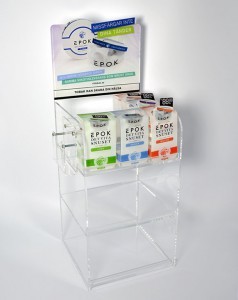
1. Idea. In a first meeting you, a project manager from Akriform and our designers and engineers, go over and discuss your thoughts and ideas. Together we develop a product that will fit your requirements.
2. Drawing. Based on what was concluded at the first meeting our designers and engineers make a drawing of what the product would look like and makes it ready for production.
3. 3D rendering. If necessary or desired, a 3D image of the drawing can be made. With a 3D image you will see exactly how the product will look like when it is completed.
4. Finished product. When you have approved the drawing / 3D image, we start production. Akriform has the capacity to do anything from one product up to thousands. Depending on how the product looks and what quantity is required, the finished product can usually be delivered about three to four weeks from the start of production.
5. Distribution. Whether the finished product will be delivered to you or anyone else we can arrange for the distribution. Upon request we can in some cases also offer storage.
To see more custom products, please visit the gallery.
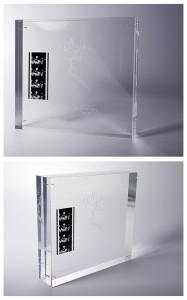
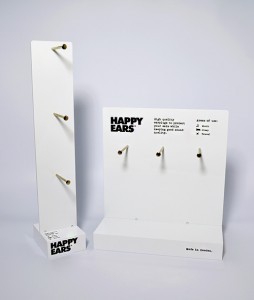